Smart Resources™ Takes The Effort
Out Of Hiring
Smart Resources™ provides the best-outsourced staffing solutions for companies in your industry.
What is Smart Resources™?
Most companies will face personnel shortages at one time or another. It may feel even more pressing as your business grows and prospers because your labor costs rise accordingly as you generate more revenue. Access to reliable and thoroughly trained workers is imperative when you rely on outsourced labor to fulfill your service model. Smart Resources™'s professional labor staffing for hire will enable you to move forward instead of cutting back.
Smart Resources™
We are an employer of choice, partnering with employers of choice. We are the leader in human capital solutions through customer alignment, innovation, and performance. We understand how our clients see value, we align to that and communicate and deliver value as they see it.
Our values
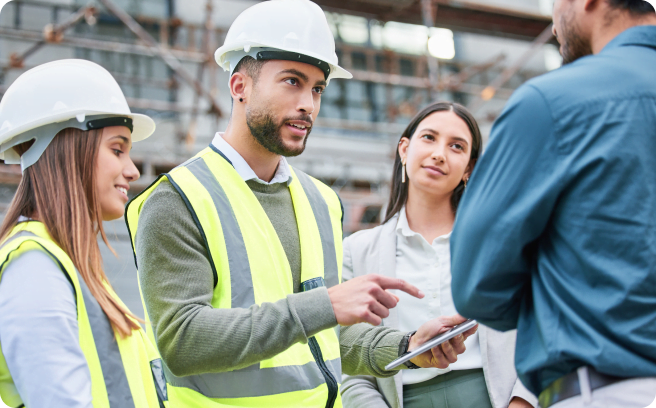
Skilled Labor Ready For Hire
Smart Resources™ started as a 3PL (third-party logistics) company that routinely faced the challenges that accompany the risks of hiring outsourced labor. We encountered inadequately trained people, insufficient numbers, and poorly managed agencies. As we repeatedly encountered the same problems, we decided it was time to fix the problem.
If your business relies on outsourced labor and you’re not working with Smart Resources™, you are probably losing money. We are the solution you need to ensure your workforce is ready to take on the work you have for the duration of the time you need. From hiring to training and managing, our people become your teams to fulfill on your deliverables. Contact us today to learn more.
Smart Resources™ Up-Levels Your Labor Force
Smart Resources™ started as a 3PL (3rd Party Logistics company) that faced the same growing pains as many businesses today. When you partner with us, you have a wealth of options designed to find qualified workers to fill your staffing needs. Labor isn’t just a money drain when you partner with Smart Resources™ – it’s one of the biggest drivers of your success.
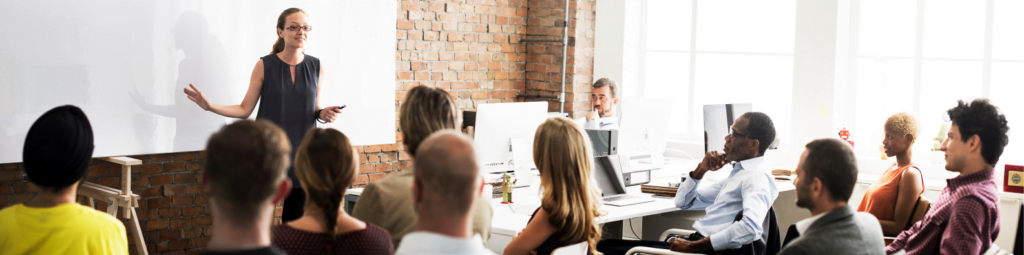
The advantages of Smart Resources™ include:
Our Staffing Options Are Ready To Work When you need Them
Because we have such a unique perspective, we have been able to forge a method that is perfect for both candidates ready to work and companies in need of effective and trained staffing. Smart Resources™ cultivates a skilled workforce because we invest in their success and strategically place them in companies that appreciate their skills and value their efforts. Our model guarantees a win-win-win scenario with all parties succeeding together. We do more than supply staffing - we deliver universal success for all of our clients.
Get The Labor Force You Need
Smart Resources™ prevents your company from spiraling due to managing a fluctuating workforce. We train and supply the full body of workers you need and provide the resources to lower cost per unit and boost efficiency. We send our strategists to your facility to evaluate your operations and needs. Once we complete the first audit, we recommend any improvements and provide a tailored labor force that increases your productivity without raising your costs. Our Strategic Alliance Program allows us to dig in effectively, find workable solutions, and outline your path to growth. Smart Resources™ makes your choice to use outsourced labor a profitable one.
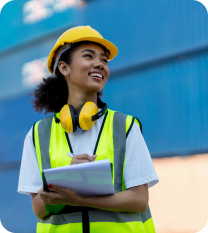
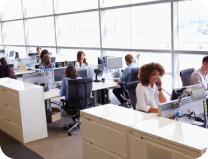
Get the Labor Force You Need
If your business relies on outsourced labor and you're not working with Smart Resources™, you are probably losing money. We are the solution you need to ensure your workforce is ready to take on the work you have for the duration of the time you need. From hiring to training and managing, our people become your teams to fulfill your deliverables. Contact us today to learn more.